Что такое плазменная резка металла и как правильно выбрать для неё аппарат
Что такое плазменная резка металла, технология процесса и критерии подбора аппаратов – об этом пойдёт речь в обзоре редакции HouseChief. Благодаря высокой точности и аккуратности получаемого результата, именно этот способ раскроя металла выходит на первый план. Тем более, на рынке строительных товаров появились бытовые аппараты подобного назначения, доступные непрофессионалам. Как выбрать такой аппарат? По каким критериям различаются модели? Обо всём этом и многом другом – в нашем материале.

Читайте в статье
- 1 Что такое плазменная резка металла, технология процесса
- 2 Для чего можно использовать плазморезку
- 3 Важное о плазматроне
- 4 Какие газы используются в плазморезке
- 5 Плюсы и минусы плазменной резки
- 6 Приборы для плазменной резки
- 7 Критерии выбора плазматрона
- 8 Практика использования плазменного резака и требования безопасности
Что такое плазменная резка металла, технология процесса
Если объяснять эту технологию простыми словами, то плазменная резка – это процесс нагрева металла струёй плазмы. Для выполнения такой задачи используют специальный аппарат – плазморез. Он формирует высокотемпературную электродугу, которая располагается между соплом резака и материалом. Температура дуги достигает 5000ºС. Но её недостаточно для эффективной резки металла, так что дополнительно в рабочую область подаётся газ, который формирует плазму с температурой до 30000ºС.

Для чего можно использовать плазморезку
Плазменная резка востребована во многих отраслях. Между прочим, она используется не только для металлических деталей, но и для обработки пластика и камня.

Плазморезкой можно кроить практически все металлы, с учётом их особенностей. Отличные результаты даёт резка низкоуглеродистых сталей. Именно по ним и рассчитываются стандартные параметры эффективности устройства. Высокоуглеродистые и легированные стали требуют усложнённого подхода с дополнительными настройками и режимами.
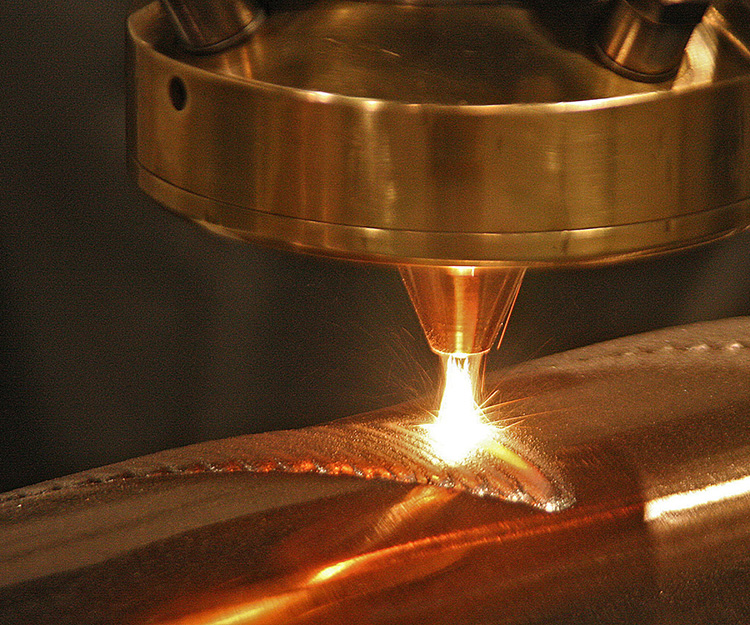
Важное о плазматроне
Задача плазматрона – объединить электродугу и газ в плазму. Для этой цели в приборе есть небольшое отверстие – сопло, через которое поступает газ. В бытовых приборах оно управляется вручную, держать его следует на весу, что усложняет процедуру раскроя. Отсутствие опыта такой работы приводит к появлению оплавленных краёв и неровностей.

Для работы резака со сталью используют азот или воздух. Чтобы выдувать оплавленный метал из шва, газ должен направляться в сопло под давлением. Для этого его закачивают в ёмкости, которые и подключаются к плазморезке.
Какие газы используются в плазморезке
Для образования плазмы могут использоваться разные газовые смеси.
- Воздушно-плазменная резка предполагает применение воздуха. Так можно обрабатывать чёрные металлы, нержавеющую сталь, латунные и медные детали.
- Кислородная резка. Этот газ применяют в профессиональном инструменте, который позволяет быстро и качественно кроить металлические листы.
- Защитные газы. Резаки с такими видами смесей используется, в том числе в ювелирном деле, так как дают высокое качество реза. Установки с использованием защитных газов стоят до 12 миллионов рублей.

Плюсы и минусы плазменной резки
Чтобы определиться с достоинствами и недостатками плазмореза, нужно сравнить его работу с ближайшими конкурентами: лазерным, гидроабразивным и кислородно-газовым резаками. В результате сравнения можно отметить такие положительные параметры:
- способность резки листов до 50 мм толщиной;
- возможность обработки любых видов металлов: от чёрных до цветных;
- высокую точность реза;
- скорость работы до 7 м/мин.;
- мобильность приборов с ручным управлением;
- минимальное количество шлака и оплава.
Но вместе с тем, присутствуют и сложности, о которых следует знать:
- сами аппараты и расходники к ним стоят довольно дорого;
- конусность реза минимальна.
Приборы для плазменной резки
На прилавках специализированных магазинов вы встретите приборы двух типов: для бесконтактной и контактной резки.
Бесконтактная резка используется для обработки пластика и натурального камня. В таких устройствах плазма образуется между соплом и электродом.

Контактная обработка подразумевает непосредственное соприкосновение электродуги с металлом. Именно такие устройства обычно приобретают для бытовых нужд.
Автоматические устройства
Такие приборы можно встретить на промышленных предприятиях. Они управляются с помощью компьютеризированных систем и позволяют точно кроить серийные листовые детали толщиной до 7 см. Обычно это очень мощные агрегаты, которые питаются от сети в 380 В.

Ручные резаки
Устройства с ручным управлением мобильны и довольно компактны. Они состоят из самого плазмотрона, шланга, трансформаторного блока и выпрямительной подстанции.
Работа с такими аппаратами может происходить в двух направлениях:
- косвенной, бесконтактной резки струёй плазмы. Этот принцип используется для неметаллических поверхностей;
- прямой контактной резки для металлических деталей.

Вес таких приборов редко превышает 25 кг, работают они от сети с обычным напряжением в 220 В. Подобные устройства универсальны и стоят от 15 тысяч рублей.
Источники питания плазматрона
Не все приборы для ручной резки работают от переменного тока. Некоторые резцы могут иметь преобразователи и усилители. Но КПД у них ниже, чем у инструментов, получающих питание постоянным током. Получается, что только такие приборы являются универсальными для резки любых изделий.
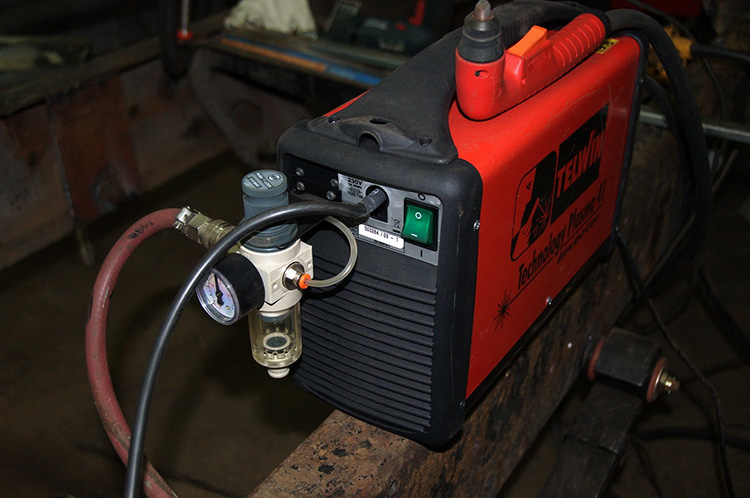
Трансформаторы весят гораздо больше, но и мощность выдают соответствующую. Они не дают сбои при перепадах напряжения. Плюс трансформаторы можно использовать постоянно, не делая перерывы на остывание. Но и счётчик электроэнергии при этом мотает киловатты с космической скоростью.
Критерии выбора плазматрона
На что следует обратить внимание при выборе инструмента? Вот существенные критерии:
- Универсальность модели. Обратите внимание на аббревиатуры в наименовании: CUT – только для металлов, TIG – аргонодуговая сварка и MMA – использование штучных электродов.
- Наличие инвертора или трансформатора в качестве источника питания. Трансформаторный более мощный, инверторный – лёгкий.
- Контактная или бесконтактная резка. Бесконтактные модели, как правило, более мощные.
- Бытовое и промышленное назначение. Разница не только в стоимости и габаритах, но и в вольтаже подключаемой сети.
- Максимально возможная толщина обработки металлов. Она зависит от мощности прибора. Для резки 1 мм толщины нержавейки и чёрных металлов нужна сила тока в 4 А, для цветных металлов – 6 А.
- Длительность рабочего цикла. Этот параметр указывается в технических характеристиках изделия и считается в процентах. Например, показатель в 60% означает, что после 6 минут работы нужно дать прибору отдыхать 4 минуты. 100% показатель имеют модели трансформаторного типа. Во многих из них для охлаждения используется водяной контур.
- Наличие встроенного или наружного компрессора. Встроенные варианты не отличаются мощностью, так что их чаще можно встретить в качестве бытовых приборов. Они более компактны.
- Удобство пользования. Этот фактор формируется из длины шланга, и чем он длиннее, тем проще работать с прибором. Но слишком длинные шланги приводят к падению мощности.


Практика использования плазменного резака и требования безопасности
Плазморез – потенциально опасный инструмент, так как использует электродугу и производит высокотемпературную плазму. По этой причине резаком не работают при отрицательных температурах. Не стоит браться за прибор при отсутствии опыта. Особенно важно следить за износом сопла и электродов. Их несвоевременная смена может привести к печальным последствиям.
Как работать плазменной резкой – в этом видеокурсе:
А у вас есть опыт работы плазменным резаком? Какую модель аппарата вы предпочитаете? Напишите об этом в комментариях!